Embrace Innovation


Technology Innovation
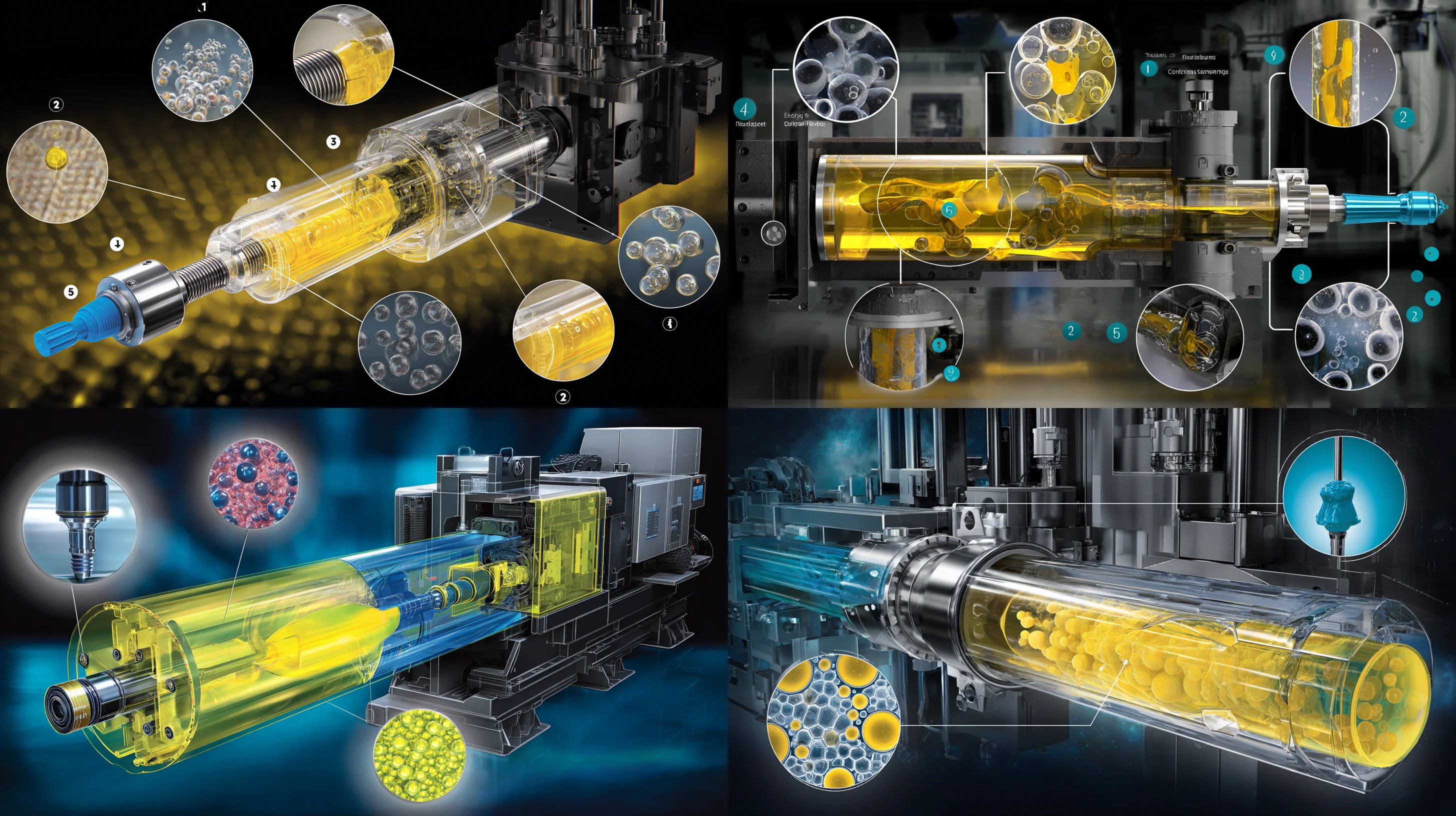
Microcellular Foaming Technology
Microcellular foaming technology?uses physical blowing agents (like N? or CO?) to create a microcellular structure during injection molding. Its core principle involves dissolving a supercritical fluid into a polymer melt. Upon injection, a sudden pressure drop nucleates bubbles, which solidify into a uniform microcellular foam during cooling.
Advantages:
Lightweight design
High dimensional precision
Reduced molding cycle time
Elimination of surface sink marks
Lower clamping force required
Applications:
Automotive, electronics, medical manufacturing and other industries
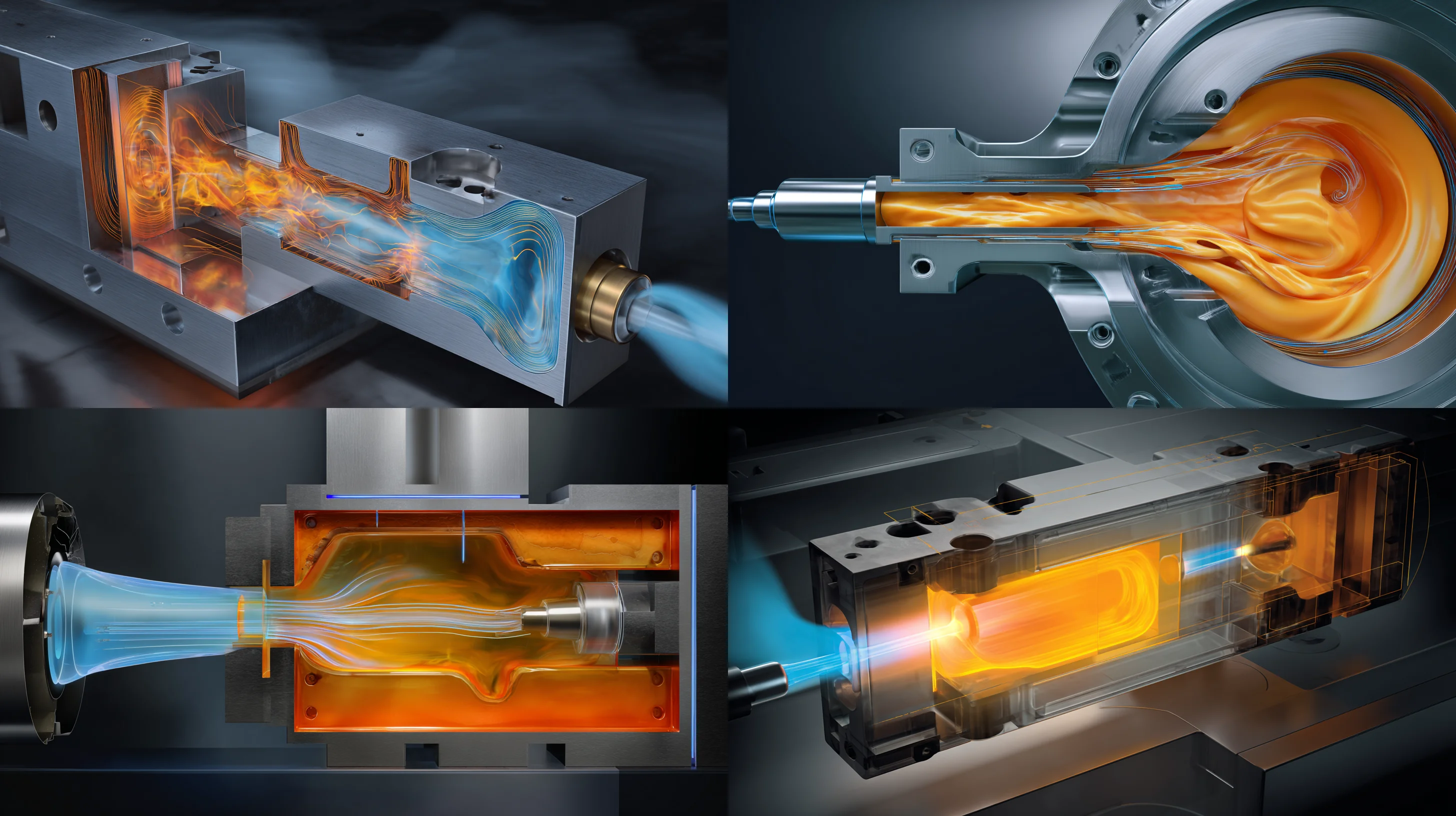
Gas-assisted injection molding (GAIM)
Gas-assisted injection molding (GAIM) is a process that optimizes injection molding by injecting high-pressure gas (typically nitrogen) into the polymer melt. It is primarily used to address defects such as sink marks and warpage in thick-walled parts.
Advantages:
Lower production costs
Improved surface finish
Greater design flexibility
Applications:
Automotive, home appliances, consumer goods and related industries
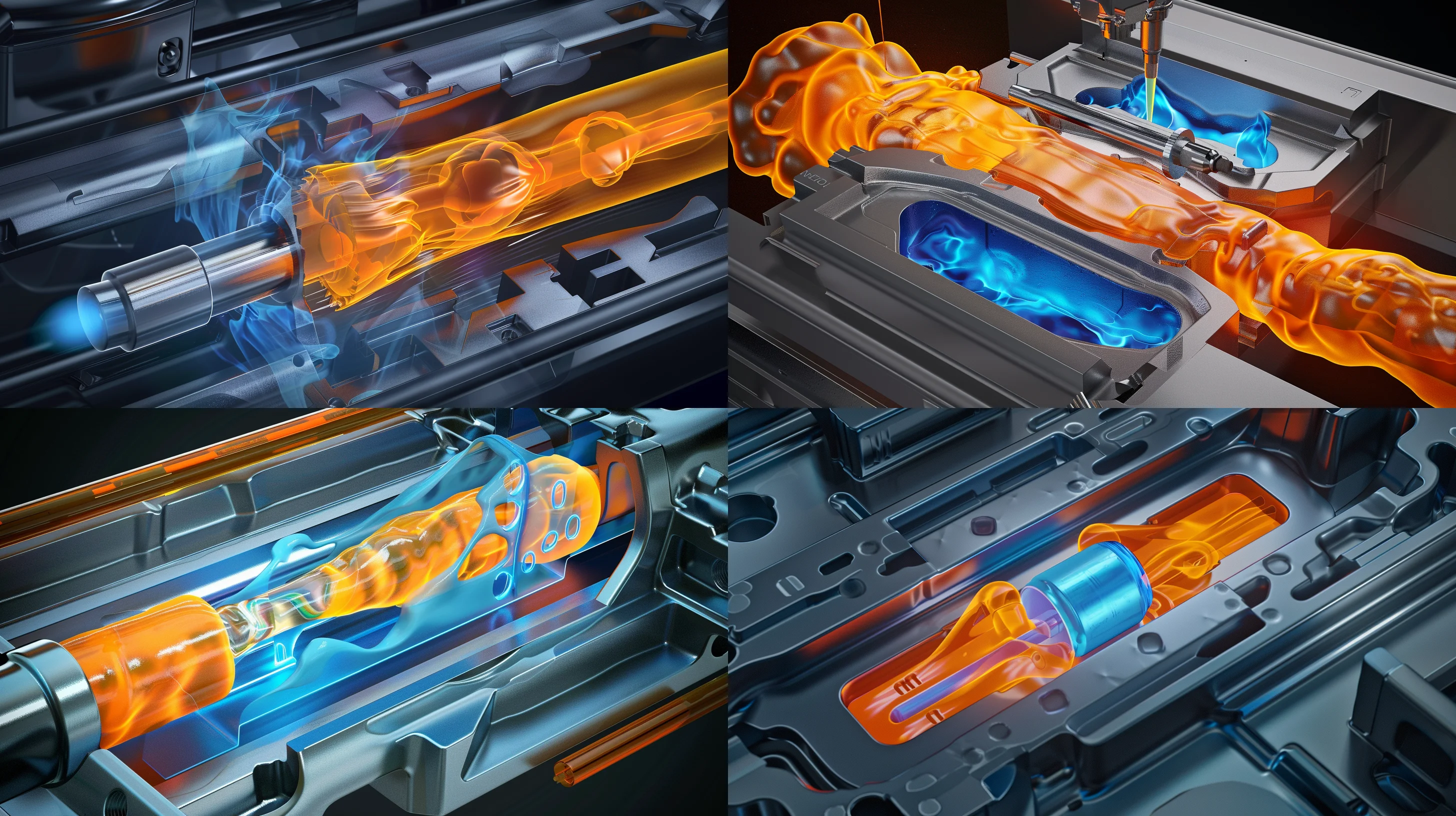
Thin-wall injection molding
Thin-wall injection molding is a precision molding process designed for parts with wall thicknesses less than 1mm or a flow length-to-thickness ratio (L/T) ≥ 100. It is primarily used to produce lightweight, high-precision miniaturized products.
Advantages:
Lightweight design
High dimensional accuracy
Reduces production costs by lowering part weight (material and molding costs)
Enhanced dimensional stability
Applications:
Automotive, consumer electronics, medical products and related fields
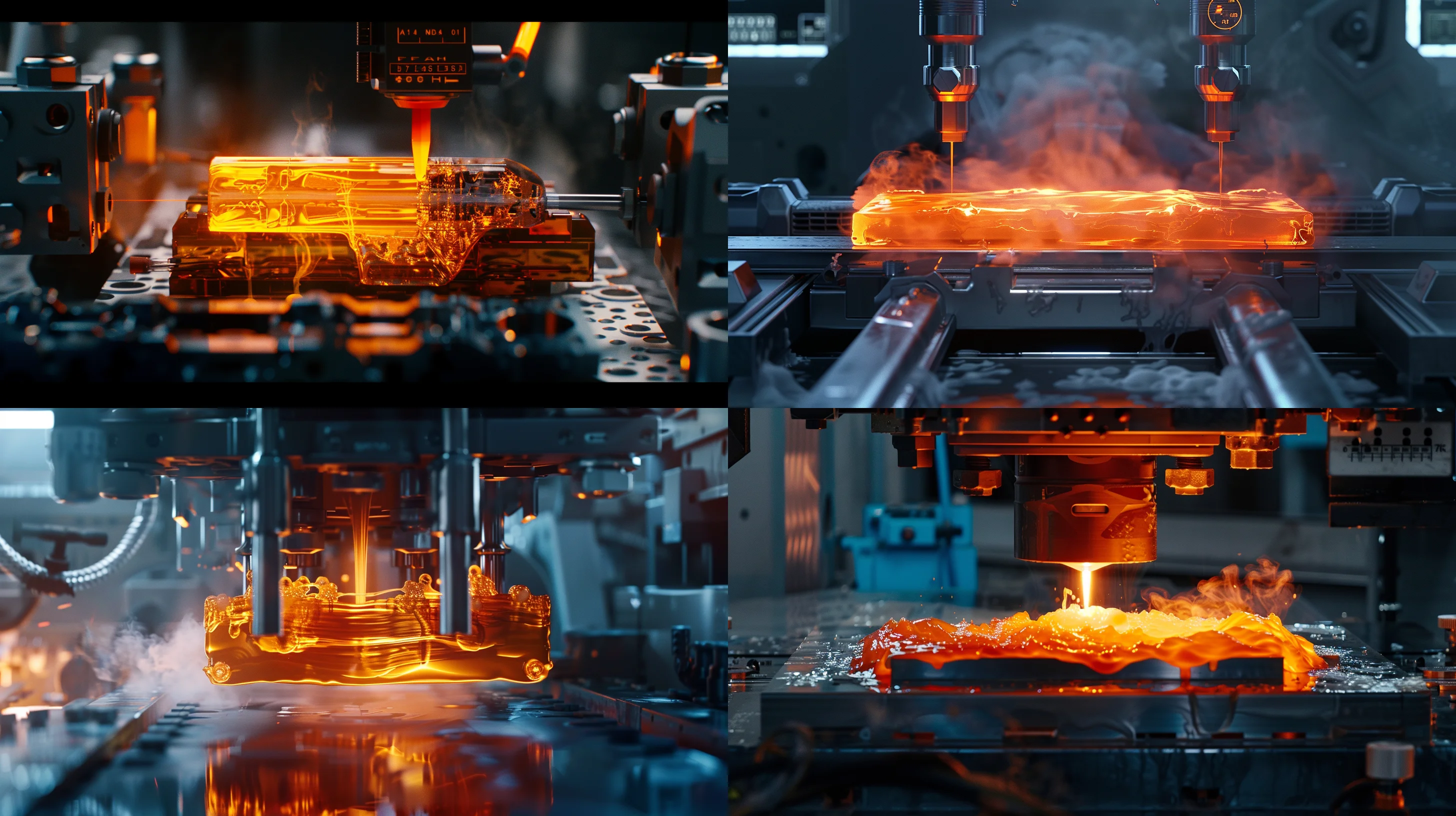
Low-pressure injection molding
Low-pressure injection molding is a forming process that injects molten plastic into a mold under low pressure (0.15–4 MPa). It is particularly suited for producing precision components with integrated skin-core composite structures.
Advantages:
High dimensional accuracy
Lightweight design
Environmentally friendly process
Improved production yield
Applications:
Automotive, electronic encapsulation, medical products and related fields
Talent Innovation
The dual-track system offers parallel advancement channels: the management track emphasizes communication, coordination and strategic decision-making, while the technical track focuses on technological innovation and problem-solving capabilities. This mechanism not only helps retain key technical talent by removing the barrier of management-track promotions but also enables specialists to stay focused on R&D, accelerating process innovation and iteration.
Management
Professional
Through the establishment of cooperation with universities, with the help of university talent advantage in-depth study of injection molding process technology innovation. At the same time, with the help of the university digital twin training system, the use of VR/AR simulation of high-risk operation scenes, reducing the cost of hands-on training of personnel.
Digital Intelligence Integration
Mold Production Dashboard integrates KPIs including annual output value, equipment yield, drilling capacity and machining tasks into a unified visual platform.
Key advantages
- Agile Capacity Control: Monitor drill utilization/OEE dynamically, auto-flag bottlenecks (e.g., <85% efficiency), accelerating task redistribution by 40%
- Data-Driven Forecasting: Sync machine output with annual targets, simulate delivery timelines proactively, achieving >95% accuracy in capacity planning
- Resource Maximization: AI-driven task scheduling based on equipment load cuts idle time by 30%, boosting average utilization to 92%+ and unlocking $500K+ annual capacity
By replacing heuristic decisions with real-time analytics, the dashboard elevates mold manufacturing to lean, delay-free production.